顧曉丹,張墩明,楊昌正
(南京大學化學化工學院,江蘇南京210093)
[摘要]為了改善水性聚丙烯酸酯樹脂涂料涂膜的耐中性鹽霧性能,在含一定量無機填料的聚丙烯酸酯樹脂水分散液中分別添加固化劑、環氧樹脂、緩蝕劑和水,對涂料配方及固化條件進行了優選,得到涂料最佳配方為:14.5 g聚丙烯酸酯樹脂,4.5 g無機混合填料(2.0 g磷酸鋅,1.5 g云母粉,1.0 g高嶺土),4.5 g固化劑C-303,2.9g環氧樹脂E-44,0.56 g苯并三氮唑,1.1 g三聚磷酸二氫鋁,配成固體質量分數為35%的涂料;將涂料涂覆于硅鋼片表面,在250℃/90 s條件下固化成膜。通過中性鹽霧試驗考察了涂料涂膜的耐蝕性能。結果顯示,最優配方及固化條件下所得涂膜的耐中性鹽霧腐蝕時間大于8 h,其耐蝕性有顯著提高。
[關鍵詞]水性涂料;聚丙烯酸酯樹脂;中性鹽霧;耐蝕性能;硅鋼
[中圖分類號]TQ630.1[文獻標識碼]A[文章編號]1001-1560(2011)12-0019-04
0·前言
不含(或少含)有機揮發物的環保型水性涂料代表著涂料的發展方向,正逐漸替代傳統的天然樹脂涂料和化學合成的油性涂料而廣泛使用,目前已占世界涂料總量的30%以上,而且還將繼續快速增長[1,2]。其中,聚丙烯酸酯樹脂是水性涂料重要的基礎樹脂,具有柔韌性好、光亮度高、耐光、耐候性佳,耐沖擊等優良性能。通過聚合單體的合理搭配可以調節樹脂的性能,同時,在分子結構中引入羧基(鹽)、羥基、醚鏈或銨鹽等親水基團可以使聚丙烯酸酯樹脂自乳化(或分散)在水中[3,4],也可以通過乳液聚合得到聚丙烯酸酯樹脂乳液[5]。然而這些親水基團結構或乳液聚合中添加的乳化劑會降低樹脂及涂層的耐水性能,用作金屬的防腐蝕絕緣涂料時會對防銹性產生不利影響。研究了水性熱固化丙烯酸涂料的黏度控制方法,并將其用于硅鋼片的防腐蝕絕緣涂層[6~8],在實際使用過程中發現,涂層的防銹性能稍差,在夏季濕熱氣候下硅鋼片易生銹,涂覆于硅鋼片表面后經5 h中性鹽霧試驗銹蝕面積達20%~30%,其性能有待進一步提高。本工作在已有研究的基礎上,重點研究了涂料配方中各組分及涂料固化條件對涂膜耐中性鹽霧性能的影響,優選出了最佳涂料配方及固化條件,顯著改善了硅鋼片涂覆后的耐中性鹽霧性能。
1·試驗
1.1基材處理
硅鋼片基材為太原鋼鐵公司50T W600/TW440型冷軋無取向硅鋼片,尺寸為0.05 cm×3.00 cm×15.00cm,使用前保存于干燥器中防銹。使用時取出,用無水乙醇擦拭2遍,去除其表面的油污和灰塵后備用。
1.2聚丙烯酸酯樹脂水分散液的制備
按文獻[6]方法制備:將聚合單體丙烯酸丁酯(工業級,使用前減壓蒸餾)10.0 g,丙烯酸羥乙酯(工業級,使用前減壓蒸餾)10.0 g,甲基丙烯酸甲酯(化學純)60.0 g,丙烯酸(化學純)20.0 g按比例混合,加入4.0 g偶氮二異丁腈(化學純,甲醇重結晶)和1.0 g十二烷基硫醇(化學純),攪勻溶解,備用。將40.0 g丁醇(分析純)加入帶有機械攪拌器、溫度計、回流冷凝管、恒壓滴液漏斗和氮氣導管的500 mL四頸瓶中,緩慢通入N2,然后開動攪拌并加熱至80℃,通過滴液漏斗一次性加入1/6的上述單體混合液,保持溫度在80~85℃反應約30 min。然后緩慢滴加剩余單體,滴加過程中保持溫度在80~85℃。滴加完畢后繼續反應4 h,然后降溫至50℃,停止通N2,通過滴液漏斗加入7.8 g二甲基乙醇胺(化學純)和47.2 g水的混合液,再攪拌30 min后出料,即得到具有較大黏度的固含量為50%的聚丙烯酸酯樹脂水分散液。
1.3涂料配制及涂層制備
涂料成分包括聚丙烯酸酯樹脂、固化劑、無機填料、環氧樹脂、緩蝕劑和水等。
(1)無機填料的超細處理將100 g磷酸鋅(工業級)、75 g云母粉(工業級)、50 g高嶺土(工業級)、675g蒸餾水和1.1 g甲基丙烯酰氧基丙基三甲氧基硅烷(工業級)混合,攪拌均勻,用QM-3SP2型行星式球磨機以轉速400 r/min球磨24 h,出料,得到固含量25%的無機混合填料水分散液。經90 Plus激光粒度儀測試,填料平均粒徑為0.5μm左右。
用同樣方法分別對磷酸鋅或中性三聚磷酸二氫鋁(工業級)作超細處理,得到固含量25%的水分散液。
(2)涂料的配制將上述聚丙烯酸酯樹脂水分散液、填料、固化劑、環氧樹脂緩蝕劑和水等按一定比例混合,配制成固體質量分數為35%的懸浮液,以轉速400 r/min球磨分散2 h后出料。
涂料各組分的用量范圍為:聚丙烯酸酯樹脂水分散液:29.0 g(聚丙烯酸酯樹脂含量為14.5 g);醚化三聚氰胺樹脂固化劑[(六甲醚化羥甲基三聚氰胺樹脂,C-303,美國氰特公司生產,固體質量分數>98%),正丁醇醚化羥甲基三聚氰胺樹脂,C-5860,江門市三木化工廠生產,固體質量分數58%)]:1.5~7.5 g;無機填料:0~7.0 g;雙酚A型環氧樹脂(E-51,環氧值0.48~0.54,E-44,環氧值0.41~0.47,藍星化工材料股份有限公司無錫樹脂廠生產):0~2.9 g;緩蝕劑植酸(質量分數70%):0~0.8 g;單寧酸(分析純):0~0.56 g;苯并三氮唑(化學純):0~0.56 g;加水調節至涂液的固體質量分數為35%。
(3)涂層制備用滴管滴數滴涂液于潔凈的硅鋼片的一端,用Webster,N.Y.,RDS 05號不銹鋼涂輥將涂液均勻涂覆在硅鋼片表面,放入恒溫鼓風烘箱中在設定溫度(150,200,250℃)固化一定時間(1~4 min),取出,備用。
1.4檢測表征
使用QNIX 15600型涂層測厚儀對固化后的涂層厚度進行測定。
依據GB/T 2423.17-93中的方法進行耐中性鹽霧性能測試,將已涂覆涂液并經過固化的硅鋼片放入LYW-015型鹽霧試驗箱樣品架上進行中性鹽霧試驗:溫度(35±2)℃,鹽霧沉降率2 mL/(80 cm2·h),試驗5~8 h后取出,觀察表面銹蝕情況。
2·結果與討論
2.1固化條件的選擇
醚化羥甲基三聚氰胺樹脂是一類廣泛使用的適用于丙烯酸樹脂體系的交聯固化劑[9],用其作固化劑,熱固性聚丙烯酸酯樹脂可以在150℃/0.5 h條件下完全固化。但固化時間過長會影響硅鋼生產線的生產效率,因此通常在爐溫350~650℃固化,時間為15~40s。本工作將固化溫度分別設定為150,200,250℃,考察不同的固化時間對涂覆硅鋼耐中性鹽霧性能的影響,測試結果見表1(涂料配方:聚丙烯酸酯樹脂14.5g,磷酸鋅2.0 g,云母粉1.5 g,高嶺土1.0 g,C-3034.5 g)。
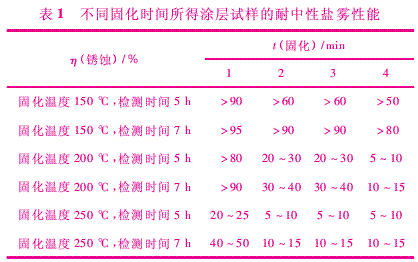
由表1可見,當固化溫度為150℃、固化時間在4min以內時涂膜的防銹性能都很差,中性鹽霧試驗5 h后銹蝕面積大于50%,7 h后銹蝕面積大于80%,說明涂層固化不徹底;當固化溫度為200℃時,固化時間達到4 min后,涂膜的固化才較為完全,7 h鹽霧試驗后銹蝕面積為10%~15%,而固化時間在3 min以內的樣品,耐鹽霧腐蝕性能較差;250℃固化試樣的耐鹽霧性能明顯改善,固化2 min時,7 h鹽霧試驗的銹蝕面積為10%~15%,以上結果表明交聯反應需要一定的時間和溫度才能完成;同時,延長加熱固化時間,有利于聚丙烯酸酯樹脂中的羧酸銨鹽發生分解,進而降低涂層的親水性,改善耐鹽霧性能。
進一步在250℃條件下,將固化時間縮短為90 s,結果顯示涂層已完全固化,經7 h鹽霧試驗后銹蝕面積為15%左右,與固化時間為2 min的樣品無明顯差別,而且這個固化條件也比較適合硅鋼線生產線涂覆固化的要求,因此,確定最佳固化條件為250℃/90 s。
2.2固化劑及其用量的選擇
分別采用六甲醚化羥甲基三聚氰胺樹脂(C-303)和正丁醚化羥甲基三聚氰胺樹脂(C-5860)作固化劑,涂料配方中其他組分不變,考察了所得涂液涂覆于硅鋼片表面經250℃/90 s固化后試樣的耐中性鹽霧性能。試驗發現:經過5 h中性鹽霧試驗后,以C-303為固化劑的試樣表面銹蝕面積較少,約為5%~10%,而以C-5860為固化劑的試樣表面銹蝕嚴重,銹蝕面積達90%以上。
造成這種耐蝕性差異的原因同2種氨基樹脂固化劑的結構有關。C-303醚化度高,分子量小,在水中有一定的溶解性,很容易均勻分散在水性聚丙烯酸酯樹脂體系中;而C-5860分子量較大,基本不溶于水,在水性聚丙烯酸酯樹脂體系中分散性較差;同時,在固化過程中,C-5860為丁醚化產品,需要更高的溫度才能固化徹底。因此,用C-303作固化劑具有更好的固化性能和耐中性鹽霧性能。
C-303固化劑用量對涂層試樣耐中性鹽霧性能的影響結果見表2。由表2可見:C-303用量為聚丙烯酸酯樹脂質量的31%~41%(即4.5~6.0 g)時,所得涂層試樣中性鹽霧試驗后的銹蝕面積最小,其用量過少或過多都會使耐鹽霧性能下降。這主要是因為C-303可以同聚丙烯酸酯樹脂中的羥基、羧基等活性基團反應,因此存在一個最佳用量,用量太多或太少都會使體系交聯度不夠,造成殘留親水基團(聚丙烯酸酯樹脂中的羥基、羧基或C-303中的甲氧基等)過多,水、鹽等容易透過涂層,從而降低了涂層的耐鹽霧性能。
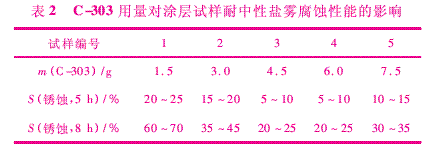
2.3添加環氧樹脂對涂層試樣耐中性鹽霧性能的影響
雙酚A型環氧樹脂具有優異的電性能、耐水性和附著性等性能[10],并可以同聚丙烯酸酯樹脂中的羥基、羧基等發生交聯反應。涂料配方中其他組分不變,不同用量環氧樹脂E-44或E-51的涂層試樣對耐鹽霧性能的影響結果見表3。
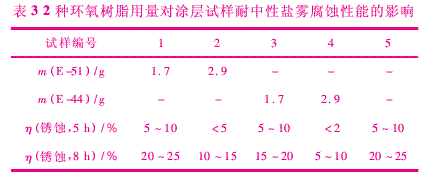
由表3可見,當環氧樹脂E-44或E-51的加入量為聚丙烯酸酯樹脂質量的12%(1.7 g)時,涂層試樣的耐鹽霧性能基本沒有提高;當環氧樹脂加入量達到聚丙烯酸酯樹脂質量的20%(2.9 g)時,涂膜的耐鹽霧性能有一定的提高,以E-44的性能最佳。此外,添加適量的環氧樹脂,還可以提高涂層的絕緣性能。
2.4添加緩蝕劑對涂層試樣耐中性鹽霧性能的影響
在涂料中分別添加單寧酸、植酸和苯并三氮唑等3種常用緩蝕劑,考察涂層試樣的抗鹽霧腐蝕性能,見表4。由表4可見,添加植酸明顯降低了涂料的pH值,使聚丙烯酸酯樹脂的水溶性下降并從水相中析出,涂料被破壞,與不加緩蝕劑的1號樣品相比,加入植酸的2號、3號涂層試樣的耐中性鹽霧性能下降;添加單寧酸的4號和5號涂料室溫放置2天后就有沉降析出,涂層的防銹性能下降;添加苯并三氮唑的6號和7號涂層試樣的耐鹽霧性能有較明顯的提高,鹽霧試驗后涂膜表面原來的點狀銹斑基本消失,這可能是苯并三氮唑在硅鋼表面形成了一層配位緩蝕膜[11]所致。由此確定理想的緩蝕劑為苯并三氮唑,最佳用量為0.56 g。
2.5填料品種及其用量對涂層耐中性鹽霧性能的影響涂層除要有一定的耐中性鹽霧腐蝕性能外,同時還要具備一定的耐高溫、電絕緣和耐磨性能等。確定m(磷酸鋅)∶m(云母粉)∶m(高嶺土)=2.0∶1.5∶1.0,考察填料用量對涂層耐鹽霧性能的影響見表5。由表5可知,在本試驗條件下,無機混合填料的添加量為0~7.0 g時,涂層的耐鹽霧性能沒有明顯變化,表明純有機樹脂涂液本身具有一定的耐中性鹽霧性能,有利于得到光滑平整的涂層,另外還可能同涂層較厚有關。
進一步考察了添加環保、無毒的防銹填料磷酸鋅或三聚磷酸二氫鋁對耐鹽霧性能的影響,結果見表6。表6的1~3號涂料中,填料總量保持不變,磷酸鋅占無機填料的比例逐漸增加,涂層的耐鹽霧性能變化不明顯。Clay等[12]認為磷酸鋅的防銹機理是磷酸鋅微溶離解而引起陽極極化和陰極極化,磷酸鋅通過離解和水解生成磷酸二代鹽離子,磷酸根與腐蝕面上的鐵離子反應,生成難溶致密的Zn2Fe(PO4)2·4H2O附著層,引起陽極極化;鋅離子與陰極區的OH-反應,生成難溶物而引起陰極極化。磷酸鋅的防銹能力主要靠它的微溶離解,單純增加填料中磷酸鋅的用量并不能有效提高涂液中磷酸鋅的微溶離解量,而且涂料的固化是在一個相對較短的時間內完成,在設定的涂料固化條件下,磷酸鋅沒有機會同硅鋼表面充分反應生成難溶致密的磷酸鹽層,因而耐鹽霧性能得不到明顯提高。對比發現,適當減少無機混合填料用量,添加占樹脂用量4%左右(0.6 g)的三聚磷酸二氫鋁(4號),涂層防銹性能有了較為明顯的提高,表面點狀銹斑明顯減少,當其添加質量為8%左右(1.1 g)時(5號),耐鹽霧性能更好。雖然三聚磷酸二氫鋁不溶于水,但是含有很多活性磷酸根,并有水解的傾向,在固化過程中與硅鋼表面反應生成難溶致密的磷酸鹽層的能力比磷酸鋅強得多[13];此外,三聚磷酸根[P3O10]5-的配位能力強,能與鐵離子反應,在硅鋼表面上生成致密的MxFey(PO4)2鈍化膜而阻緩腐蝕(M為金屬),從而提高了試樣的耐中性鹽霧性能。
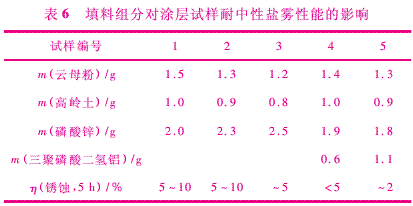
2.6優化涂料配方及固化條件
綜上,以表6中5號配方為基礎,為保證涂液中無機物的質量分數,將無機填料仍調整為4.5 g,得到最優配方為:14.5 g聚丙烯酸酯樹脂,4.5 g無機混合填料(磷酸鋅2.0 g,云母粉1.5 g,高嶺土1.0 g),4.5 g固化劑C-303,2.9 g環氧樹脂E-44,0.56 g苯并三氮唑,1.1 g三聚磷酸二氫鋁,配成固體質量分數為35%的涂料。將此涂料涂覆于硅鋼片表面,于250℃/90 s固化后的中性鹽霧試驗顯示:經8 h鹽霧試驗涂層試樣表面無銹蝕,耐中性鹽霧性能有了很大提高。
3·結論
(1)在含一定量無機填料的聚丙烯酸酯樹脂水分散液中,加入占樹脂質量35%左右的六甲醚化三聚氰胺樹脂C-303為固化劑,得到的水性聚丙烯酸酯樹脂涂料,可以在250℃/90 s條件下在硅鋼片表面固化為具有一定耐中性鹽霧性能的涂層。
(2)在涂料配方中添加適量的雙酚A型環氧樹脂E-44、苯并三氮唑和三聚磷酸二氫鋁可以提高涂層的耐中性鹽霧性能。得到的優化涂料配方為:14.5 g聚丙烯酸酯樹脂,4.5 g無機混合填料(磷酸鋅2.0 g,云母粉1.5 g,高嶺土1.0 g),4.5 g固化劑C-303,2.9 g環氧樹脂E-44,0.56 g苯并三氮唑,1.1 g三聚磷酸二氫鋁,配成固體質量分數為35%的涂料。將此涂料涂覆于硅鋼片表面,于250℃/90 s固化后,涂層的耐中性鹽霧時間大于8 h。
[參考文獻]
[1]趙金榜.國內外涂料工業現狀及發展趨勢(一)———世界涂料工業現狀及發展趨勢[J].電鍍與涂飾,2006,25(1):51~54.
[2]鄭素榮,王尉安,楊仕軍.綠色環保型涂料的研發進展[J].廣州化工,2006,34(2):63~64,69.
[3]伊洋,胡應模,沈樂欣,等.陽離子型水性丙烯酸樹脂合成工藝研究[J].上海涂料,2009,47(6):19~21.
[4]Kanou K,Amano J,Sakai N.Aqueous pigment dispersion,water-soluble
resin,production process of the resin,andequipment suitable for use
with the dispersion:EP,0803554A2[P].1996-04-22.
[5]李亞鵬,陳獻工,王靜媛,等.丙烯酸酯水性樹脂乳液及其合成方法和用途:中國,101565484A[P].2009-05-26.
[6]任秋賢,楊昌正.水性熱固性丙烯酸涂料粘度的控制[J].涂料工業,2001,31(8):15~17.
[7]楊昌正,任秋賢,蔣錫群,等.一種水性丙烯酸樹脂防銹、絕緣涂料及其制法:中國,1317526A[P].2001-04-17.
[8]韓曉光,張墩明.無取向硅鋼絕緣涂料的研究進展[J].科技信息,2008(25):40~41.
[9]魏雨.醚化三聚氰胺樹脂的制備及其在涂料中的應用[J].上海涂料,2007,45(1):22~25.
[10]孫曼靈.環氧樹脂應用原理與技術[M].北京:機械工業出版社,2002:4~5.
[11]李曉偉,高延敏.碳酸氫鈉溶液中苯并三氮唑對A3鋼緩蝕作用的研究[J].全面腐蝕控制,2009,23(1):13~15.
[12]Clay H F,Cox J H.Chromate and phosphate pigments in anticorrosive
primers[J].Journal of the Oil and ColourChemists’Association,1973,56(1):13~16.
[13]Bittner A.Water-based protective coatings with phosphate pigments
[J].Journal of the Oil and Colour Chemists’As-sociation,1988,71(4):97~102.[編校:魏兆軍]